Valves are pipeline accessories used to open and close pipelines, control the flow direction, and adjust and control the parameters (temperature, pressure and flow) of the conveying medium. They play a pivotal role. Let’s take a look at different types of fluid valves and their characteristics.
Ball Valve
Ball valves are available in two designs, float and trunnion. The floating ball valve will generate high operating torque at high pressure or large pipe diameter, but the sealing performance is better. Ball valves are not suitable for throttling because, when the valve is partially open, its sealing surfaces are damaged by exposure to the process fluid. For critical operations, consideration should be given to purchasing a ball valve with ball seat and stem lubrication fittings, as lubrication can prevent minor leakage and reduce operating torque. If the valve is required to have both shut-off and relief functions, it should Ball bleed hole independent of lubrication fitting.
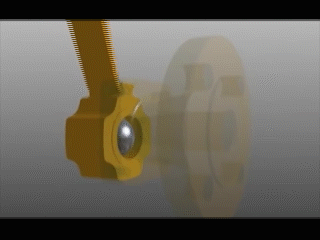
When the operating temperature is between -29°C and 200°C, most manual ball valves are suitable for the operation of hydrocarbon and utility systems; for ball valves used above 100°C, careful consideration should be given to the temperature limit of the soft sealing material during application. ℃ or above; in the case of high temperature or serious abrasion operations, the application of metal-sealed ball valves should be considered, but it should be noted that the operating torque must be increased.
Gate Valve
Gate valves are suitable for most switching operations, vibration-free hydrocarbons, and utilities over all temperature ranges. Unless the stem packing is carefully adjusted, gate valves have better torque characteristics than ball and plug valves, but do not have the convenient operating characteristics of a 90-degree turn action. Manually operated gate valves of size DN50 (2in) or larger should be equipped with a resilient gate or expansion gate. Wedge gate valves generally do not have cavity overpressure protection. Unprotected rising stem gate valves are not recommended because marine environments can corrode exposed stems and threads, making valve operation difficult and easily damaging stem packing. Gate valves with reverse-acting plates are suitable for automatic shut-off system operation. Simple push-pull operators are available for these valves, thus avoiding the complex lever cams normally required for the ball and plug valves. All moving parts with power operators on the gate valve can be closed off, eliminating contamination due to paint and corrosion products. Gate valves cannot be used in throttling operations, especially for fluids containing sand, because throttling can damage the valve sealing surfaces. The operating temperature of the soft-sealed gate valve is limited by the sealing material.
Check Valve
There are various forms of check valves: including swing type, lift type, ball type, piston type, etc.
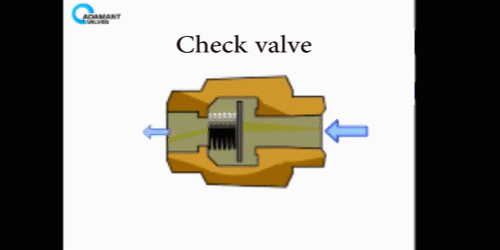
The fully open swing check valve is suitable for most non-fluctuating conditions. Swing check valves should use a screw or bolted bonnet for inspection and repair of the disc and seat. In many cases, repairable high-pressure swing check valves on pipelines can be as small as DN65 (2.5NPS) or DN80 (3NPS).
Lift check valves can only be used to handle clean fluids on small diameter (DN 40), high pressure pipelines. Lift check valves can be designed for use in horizontal or vertical pipelines, but the two are not interchangeable. Because lift check valves are usually gravity operated, they can become clogged by paraffin or debris.
Ball check valves are very similar to lift check valves. Since the ball is lifted by hydraulic pressure, this type of check valve does not have the tendency of the flap to close the slam like a rotary check valve. Therefore, in pipes up to DN 50 (2 in), it is better for cleaning fluids that change direction frequently.
Piston check valves are equipped with an orifice plate to control the movement of the piston. Orifice plates for liquids are much larger than those for gases. Piston check valves designed for gas lines should not be used for liquid service unless the orifice plate in the piston is replaced.
Butterfly valve
Common Butterfly Valves are suitable for rough throttling and low pressure, hydrocarbon free, non-hazardous operations, they are not suitable for use as critical shut-off valves for vessels, tanks, etc. In working conditions where the temperature is higher than 65°C or the pressure class is higher than ASME 150 or hazardous fluids, the non-linear butterfly valve should be applied. Because only a small torque is needed to vibrate the butterfly valve open, the handle should be equipped with a locking device.
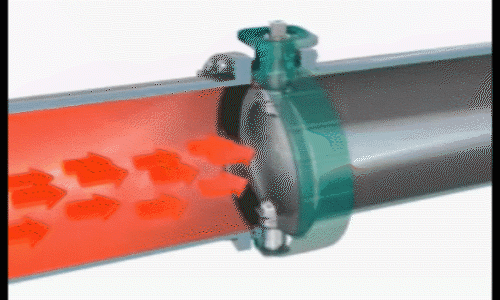
Globe valve
Globe valve, also known as Shut-off valve, is a forced sealing valve. When the valve is closed, pressure must be applied to the disc to force the sealing surface against leakage. When the medium enters the valve from under the valve disc, the resistance that the operating force needs to overcome is the friction force between the valve stem and the packing and the thrust generated by the pressure of the medium. The force to close the valve is greater than the force to open the valve, so the diameter of the valve stem should be larger, otherwise, the valve stem top bending failure will occur. When the globe valve is opened, the opening height of the valve disc is 25%~30% of the nominal diameter. The flow rate has reached the maximum, indicating that the valve has reached the fully open position. Therefore, the fully open position of the globe valve should be determined by the stroke of the valve disc.
Diaphragm Valve
This valve uses a diaphragm made of synthetic rubber to connect to the valve stem, and closing the valve is accomplished by pressing the diaphragm against a metal boss (which is part of the valve body). Diaphragm valves are primarily used in low pressure water 1400 kPag (200 psig or less) operations, and they are especially suitable for systems containing a sand and other solids.
Plug Valve
Plug valves have the same range of use and similar operating temperature limits as ball valves. Plug valves with 90-degree rotation operation are available in lubricated and non-lubricated designs. Lubricated plug valves must be lubricated regularly to ensure good sealing and easy operation. The number of times of oiling depends on the conditions of use. Its lubricating function is a solution to preventing valve jamming.
In non-lubricated designs, its sealing is done with Teflon, nylon and other soft materials. They do not require frequent maintenance and lubrication, but when the valve is set in one position for an extended period of time, it becomes difficult to turn it again. Based on these characteristics, it should be selected according to the specific use environment (condition).
Needle valve
Needle valves are basically small globe valves. They are often used as shut-off valves for instrumentation and pressure gauges, for small flow throttling of instrument air, natural gas, and hydraulic fluids, and for reducing pressure fluctuations in instrumentation piping. The needle valve has a small channel and can be easily blocked, so take this into consideration when using it.
For more information on different types of sanitary valves, please visit http://www.adamantvalves.com/.