Valve Characteristics
The use characteristics of the valve determine its main performance and use range. The use characteristics of the valve include: valve category (closed-circuit valve, regulating valve, safety valve, etc.), product type (gate valve, globe valve, butterfly valve, ball valve, etc.), valve main parts (valve body, valve cover, valve stem, valve disc, sealing surface) material, valve rotation method, etc.
The structural characteristics of the valve determine the installation, repair, maintenance and other methods of the valve. The structural characteristics include: the structural length and overall height of the valve, the connection form with the pipeline (flange connection, threaded connection, clamp connection, external thread connection, welding end connection, etc.), the form of the sealing surface (insert ring, thread connection, etc.) ring, surfacing, spray welding, valve body), valve stem structure (rotating rod, lifting rod), etc.
How to Choose the Valve?
- Clarify the purpose of the valve in the equipment or device, and determine the working conditions of the valve: applicable medium, working pressure, working temperature, etc.
- Determine the nominal diameter and connection method of the pipeline connected to the valve: flange, thread, welding, etc.
- Determine the way to operate the valve: manual, electric, electromagnetic, pneumatic or hydraulic, electrical linkage or electro-hydraulic linkage, etc.
- Determine the material of the shell and internal parts of the selected valve (according to the medium conveyed by the pipeline, working pressure and working temperature): gray cast iron, malleable cast iron, ductile iron, carbon steel, alloy steel, stainless acid-resistant steel, copper alloy, etc.
- Select the category of the valve: closed-circuit valve, regulating valve, safety valve, etc.
- Determine the type of valve: gate valve, globe valve, ball valve, butterfly valve, throttle valve, safety valve, pressure reducing valve, steam trap, etc.
- Determine the parameters of the valve: For automatic valves, first determine the allowable flow resistance, discharge capacity, back pressure, etc. according to different needs, and then determine the nominal diameter of the pipeline and the diameter of the valve seat hole.
- Determine the geometric parameters of the required valve: structural length, flange connection form and size, valve height direction size after opening and closing, size and number of bolt holes connected, overall valve size, etc.
- Use the available information to select the appropriate valve product: valve product catalog, valve product sample, etc.
Principles to be Followed While Choosing
Valve for flow control
Usually, the valve that is easy to adjust the flow is selected as the control flow. Downward closing valves, such as globe valves, are suitable for this purpose because of the proportional relationship between the size of the seat and the travel of the closing member.
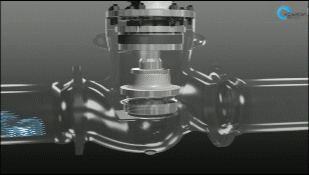
Rotary valves (plug valves, butterfly valves, ball valves) and flexible body valves (pinch valves, diaphragm valves) can also be used for throttling control, but usually only within a limited range of valve sizes.
The gate valve uses the disc-shaped gate to make a transverse movement to the circular valve seat mouth. It can control the flow well only when it is close to the closed position, so it is usually not used for flow control.
Valve for reversing flow
Valves for this use may have three or more passages, depending on the needs of the diverter. Plug valves and ball valves are more suitable for this purpose, so most of the valves used for reversing and diverting are selected from one of these types of valves. In some cases, however, other types of valves can also be used for reversing and diverting, as long as two or more valves are properly connected to each other.
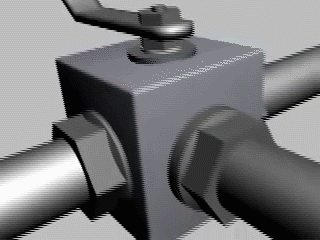
Valves for media with suspended particles
When there are suspended particles in the medium, it is most suitable to use a valve whose closing member slides along the sealing surface with a wiping effect. If the back-and-forth movement of the closure member to the valve seat is vertical, particles may be trapped, so this valve is only suitable for substantially clean media unless the sealing face material can allow the particles to be embedded. The ball valve and the plug valve have a wiping effect on the sealing surface during the opening and closing process, so they are suitable for use in the medium with suspended particles.
Conclusion
At present, whether in the pipeline system of petroleum, chemical industry or other industries, valve applications, operating frequencies and services are ever-changing. To control or prevent even small leaks, the most important and critical equipment is the valve. The ultimate control of the pipeline is the valve, which is unique in service and has reliable performance in each field. For more information of high-quality sanitary valves, please visit https://www.adamantvalves.com/.