The production of valves is a complex yet simple process. The production cycle of ordinary valves such as gate valves, ball valves, globe valves, butterfly valves and check valves is generally three days. After the valve is produced, it must undergo various performance tests, the most important of which is the pressure test.
The pressure test is to test whether the pressure value that the valve can withstand meets the requirements of production regulations. The following are the precautions for valve pressure testing in general:
(1) In general, the valve is not tested for strength unless the valve body and bonnet are repaired or corroded. For the safety valve, its constant pressure, reseating pressure and other tests should comply with the regulations of its manual and relevant regulations.
(2) The strength and tightness test should be carried out when the valve is installed. Low-pressure valves are generally inspected for 20%, and if any of them are unqualified, 100% inspection should be done; medium and high-pressure valves should be inspected 100%.
(3) During the test, the valve installation position should be in a direction that can be easily checked.
(4) For valves in the form of welded connections, if the pressure test cannot be performed with a blind plate, a conical seal or an O-ring seal can be used.
(5) The valve air should be excluded as much as possible during the hydraulic test.
(6) The pressure should be gradually increased during the test, and rapid and sudden pressure increase is not allowed.
(7) The duration of the strength test and the sealing test is generally 2-3min, sometimes longer. The test time of small-diameter valves is generally shorter than that of large-diameter valves. If there is any doubt during the test, the test time can be extended. During the strength test, the valve body and valve cover are not allowed to sweat or leak. General valves only need to be tested once, and safety valves and high-pressure valves need to be tested twice.
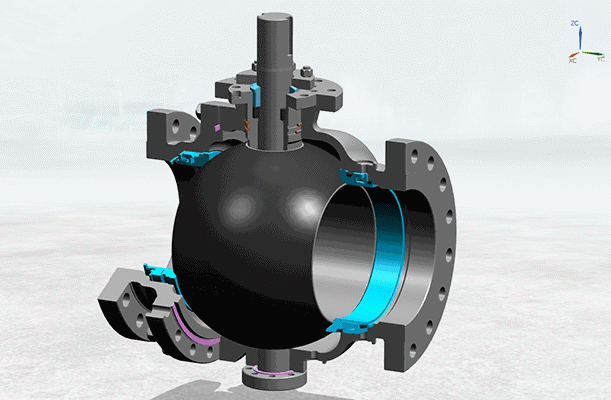
(8) The tightness test of the closing parts of the throttle valve is not carried out, but the strength test and the tightness test of the packing and gasket shall be carried out.
(9) During the pressure test, only one person is required to close the valve with normal force, instead of using tools such as levers (except for torque wrenches); when the diameter of the handwheel is greater than or equal to 320mm, two people are allowed to close together.
(10) During the strength and tightness test of the main valve, if the closing part of the main valve is opened, the bypass valve installed on the main valve should also be opened.
(11) When the cast iron valve is tested for strength, tap the valve body and bonnet with a copper hammer to check for leakage.
(12) When the valve is tested, except for the plug valve that allows the sealing surface to be oiled, other valves are not allowed to be oiled on the sealing surface.
(13) During the pressure test of the valve, the pressing force of the blind plate on the valve should not be too large, so as not to deform the valve and affect the test result.
(14) After the valve pressure test is completed, the water in the valve should be removed in time and the valve should be wiped clean.